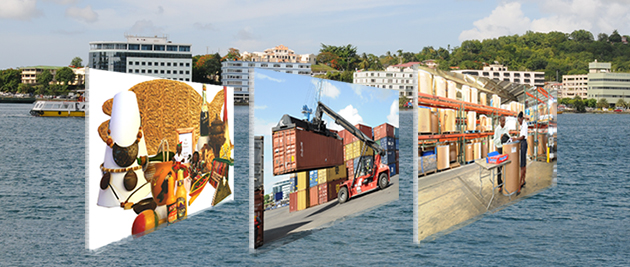
In the last decades, Quality and its management have become topical issues for most, if not all businesses. As markets have become more competitive, the concept of Quality Management implementation is now regarded as key component to business success.
But some may ask, what exactly is Quality Management, and all those terms that accompany it - such as ISO 9001, Quality Assurance, Quality Control, Process Mapping, Document Control / Management? These still seem very unclear to many!
Simply put, "Quality" is about being able to meet, and where possible, exceed the needs and expectations of your customers. It is much more than simply producing a product that works properly, it is more than expecting the market to absorb whatever your business delivers and it is certainly more than surviving in the business arena. Quality allows you to determine what your customers require - meaning what is expected, how it is expected, when, where and to whom it goes, in addition to understanding why the customer requires your product, so that you can put into perspective, and put in place the product or service attributes that will fulfill the customers' stated needs or requirements, and their expectations.
ISO 8402-1986 standard defines quality as "the totality of features and characteristics of a product or service that bears its ability to satisfy stated or implied needs." A more current ISO Standard (ISO 9000:2000) for Quality Management Systems-Fundamentals and Vocabulary defines quality as "the degree to which a set of inherent characteristics fulfills requirements". This ultimately means, you put yourself in your customers' shoes and think as your customer would, in order to meet and exceed their requirements. For example if you were to buy your own product, would you be satisfied or more so, delighted with the product performance, appearance, availability, delivery, reliability, maintainability, cost effectiveness and price.
From the perspective of the Quality Standards that the product or service adheres to, one should consider whether the product or service is safe, healthy, fit for use, wholesome, environmentally friendly, technically sound i.e. the product or service can pass the required technical assessments or tests associated with it. Some of these may very well reflect the customers' unstated but expected needs. If the product or service does not deliver those, then it is sub-standard.
Quality therefore represents all the features of a product or service that affect its ability to satisfy or even delight your customers. Whether some business places want to believe it or not, your customers are the reason why you exist. Quality systems ensure your customer needs and product specifications are met, and consequently business viability is enhanced.
The truth about delivering great quality is that it is the responsibility of everyone in the business. While we focus on meeting customer needs, it is not only up to the front line staff. Good Quality is achieved by more than just the people at the point of contact with the customer. They go beyond the front line. Think of the man in a battlefield and the strategies that must be defined and implemented to achieve a victory.
Great services and product delivery depend on the kinds of strategies and processes we have in place. Strategies inform the actions to be followed to achieve quality objectives. Then processes are supported by procedure; where a procedure details steps required to perform an activity or task (by whom, why, when, where). A process very simply put, is a combination of procedures, and the interaction of these processes makes up your business system.
Therein lies the need for Quality Management. Producing great products and services of the required quality do not happen by accident! One should Plan for Good Quality. There are processes, such as the production process, which have to be properly managed. Quality management therefore is concerned with controlling activities with the aim that the products and services will be fit for their purpose and meet technical specifications or other specifications for that matter.
There are fundamentally two main parts to Quality Management (i) Quality Assurance and (ii) Quality Control; and then again I should add Quality Planning.
Quality Assurance is about how a business can design the way a product or service is produced or delivered to minimize the chances of a sub-standard end result /outcome. The focus of Quality Assurance is on the design / development stages. Why is this necessary, you may ask?
If the processes and procedures used to produce a product or service are not tightly controlled (in other words, we just let "things" happen), the attributes of the product or service cannot be guaranteed with any certainty. Quality must be "Built -in". If the Production process is more controlled and checked to give certain "assurances", then there is less need for inspection of the end product (Quality Control).
Quality Control is the traditional way of managing for quality, by checking or reviewing work that has been done. It includes inspection, sampling and testing. Quality control is mainly about "detecting" defective output - rather than preventing it. This is however very expensive - scrapping, reworking, re-submitting, and possible "fire-fighting". These are referred to as the cost of poor quality. Other costs of poor quality include the possibility of lawsuits and loss of reputation. This is why Quality Management has adopted the more pro-active step of Quality Assurance.
Quality Assurance involves not only good process development, but the development of close relationships with customers (external and internal to your business) and suppliers. Suppliers to your business must also understand exactly what is required of them - and deliver!
Essentially Quality Management is about a kind of business philosophy which emphasizes the need for all parts of a business to continuously look for ways to improve quality and maintain the initiatives that support good business practices.
The Small Enterprise Development Unit within the Ministry of Commerce, Industry and Consumer Affairs recognizes the significance of proper quality management to the survival of micro and small enterprises. To this end it has embarked on an initiative to sensitize and encourage enterprise owners on quality management issues. The initiative includes training in quality management and on site assessment of quality issues. A Business Development Officer is assigned to the respective enterprise to develop a strategic plan to address and maintain proper quality practices.
Submitted by Roycelyn St. Hill Howell and edited by Perle Alcindor & Barbara Innocent- Charles (Business Development Officers, SEDU, Ministry of Commerce, Industry and Consumer Affairs)